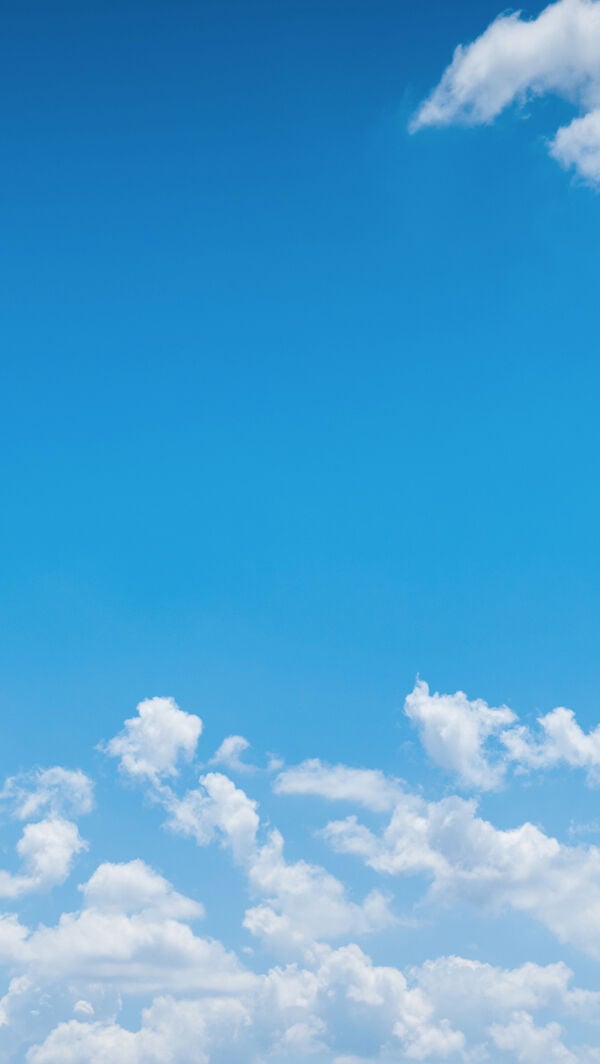
CLIMATE
ACCELERATING THE CLIMATE TRANSITION
Reducing carbon footprint
Limiting global warming to less than 2°C is everyone's business. Berluti must set an example and take a path that is compatible with the Paris Agreement signed at the end of COP21, to ensure it contributes to the European objective of carbon neutrality in 2050. From product design to distribution, including manufacture and transport, constant effort must be made at every stage to limit their impact. The indicators put in place allow precise monitoring of the progress made. Berluti has committed to reducing its greenhouse gas emissions by 51% by 2030, compared to 2019.
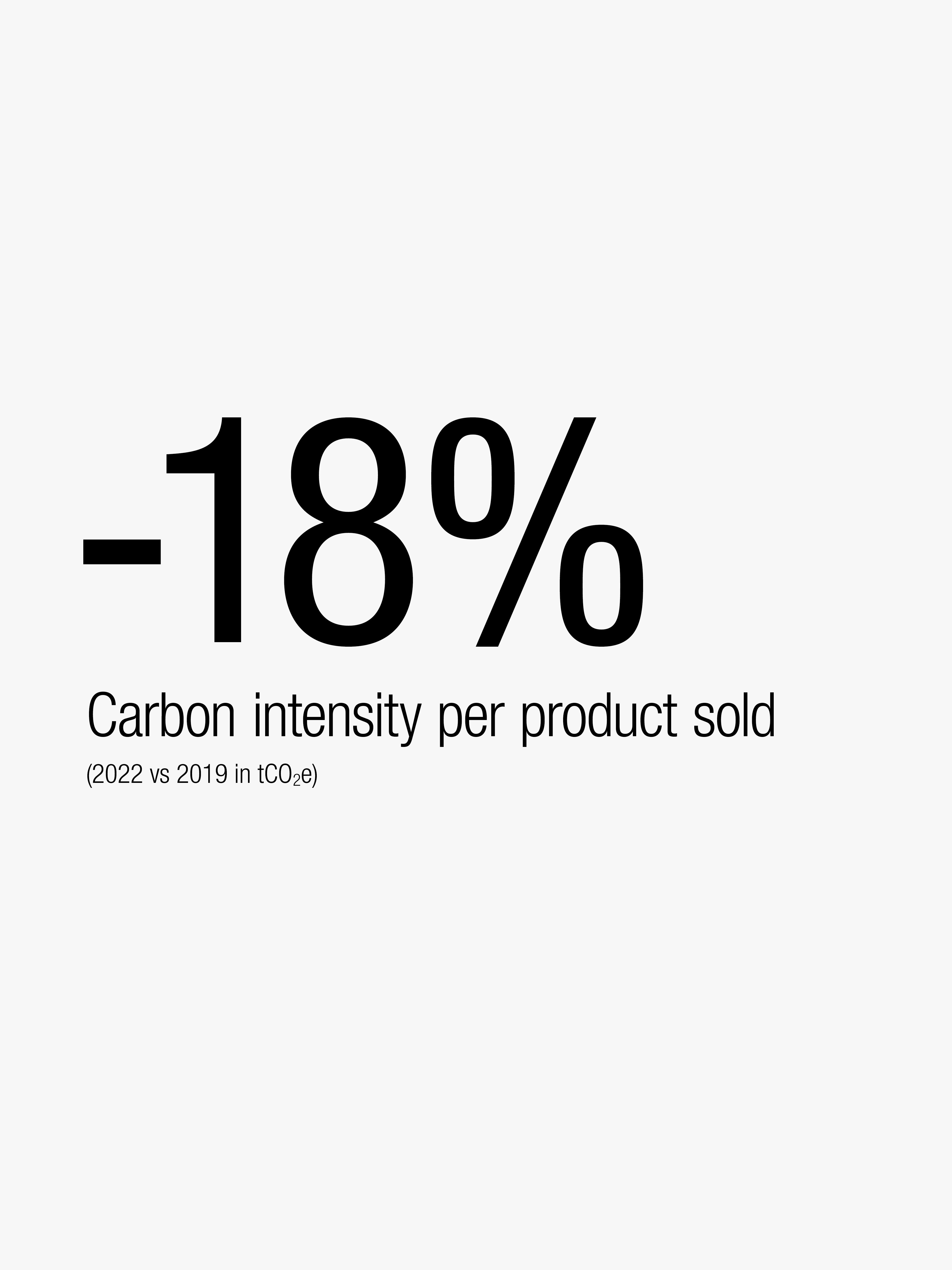
CONDUCTING THE CARBON ASSESSMENT
After performing an initial carbon assessment on the year 2019, Berluti called on the Quantis consultancy once again to repeat the exercise on all three of its scopes* in 2022. Collecting this information made it possible to determine our principal sources of emissions: materials procurement, and to a lesser degree logistics, in-store energy consumption, business trips, and employee commutes. The resulting emissions reduction trajectory corresponds with SBTi (Science Based Targets initiative) standards. The reduction projects are tracked within each department and reviewed at Environment Committee meetings on a quarterly basis, and have already made it possible to reduce the absolute value of CO2 emissions in 2022 by 10% compared to 2019.
* Scopes are the perimeters within which the organization’s greenhouse gas emissions are studied. Scope 1 includes direct emissions resulting from the production process. Scope 2 covers indirect emissions relating to the energy consumed on the sites. Scope 3 takes into account all emissions connected to the product’s life cycle (from the extraction of resources to the end of its life).
INCREASINGLY RESPONSIBLE ROAD TRANSPORTS
Since May of 2023, low-carbon transports have been used to carry products from Manifattura Berluti in Italy to the Berluti logistics center in France. The vehicles making this journey are no longer powered by diesel, but by B100, a 100% plant-based fuel composed of oils, and by biogas, a fuel created through the anaerobic digestion of waste primarily produced by agriculture.
Meanwhile, since June of 2023, deliveries to our Paris-based stores have been made using B100-fueled vehicles and, for the last six miles, electric trucks. These changes not only reduce our CO2 emissions, but also our logistics-related particulate emissions.
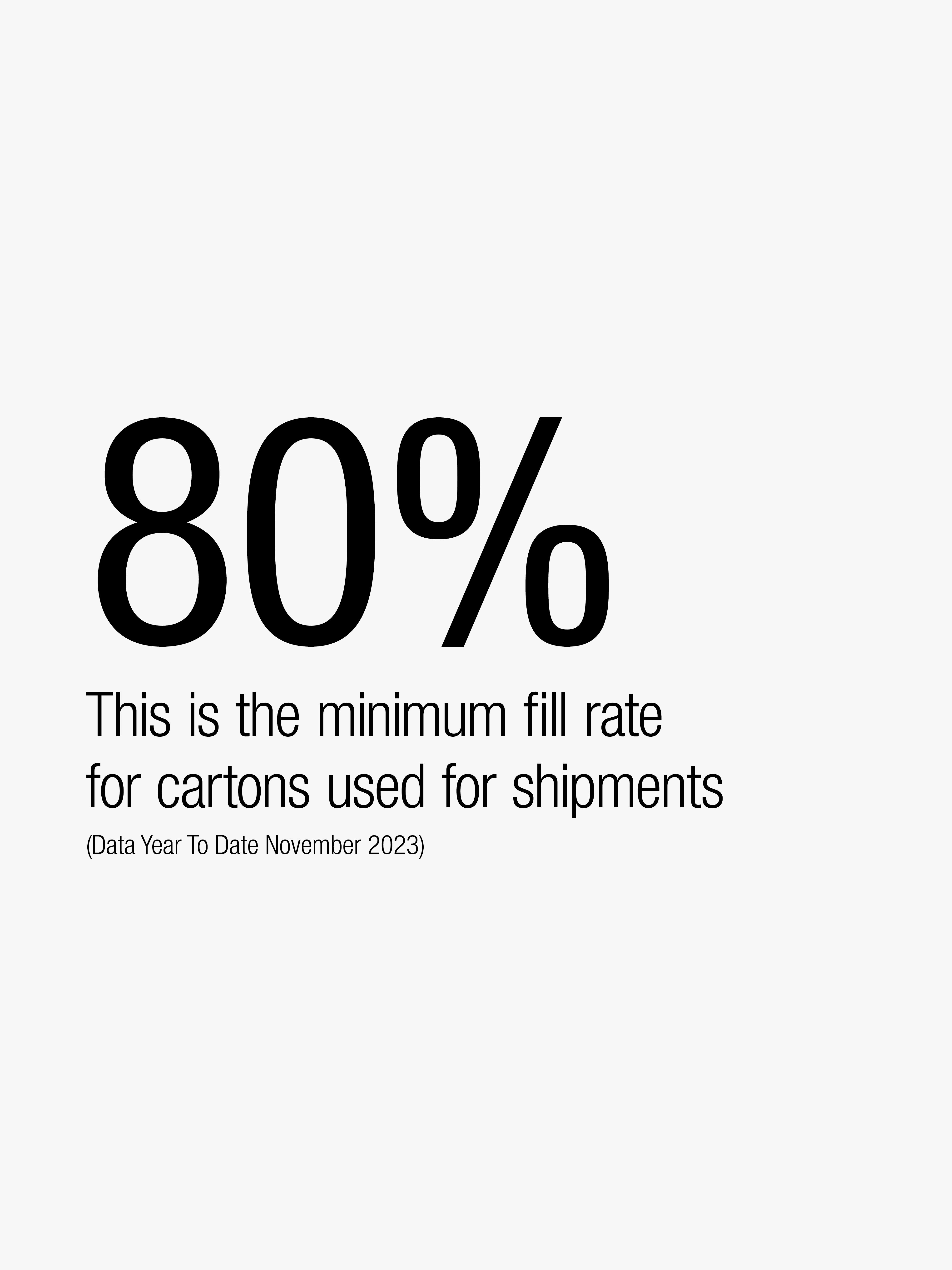
Environmentally conscious sites
Worldwide, just under seventy stores offer customers Berluti leather goods, accessories and ready-to-wear collections. But the heart of the company is at the Berluti Manifattura in Ferrara, Italy, which is dedicated to the production of shoes and leather goods. Wherever Berluti operates, it strives to favor the use of clean energy, to limit its consumption and cut waste emissions.
Berluti Manifattura certified ISO 14001
Carbon performance is now of utmost importance in the decisions that govern the future of the Berluti Manifattura. After a series of audits conducted in 2021, the 8,000 m2 space has obtained ISO 14001 certification. This standard specifies the framework for implementing an environmental management system. Collecting reliable environmental data and identifying the global warming risks and opportunities that could impact operations are among the audit points of ISO 14001 certification. By taking this approach, the company will be able to anticipate developments and take fuller control over its activities, products and services to better respect the environment. It attests to the commitment of the entire organization to the environment and more efficient use of natural resources.
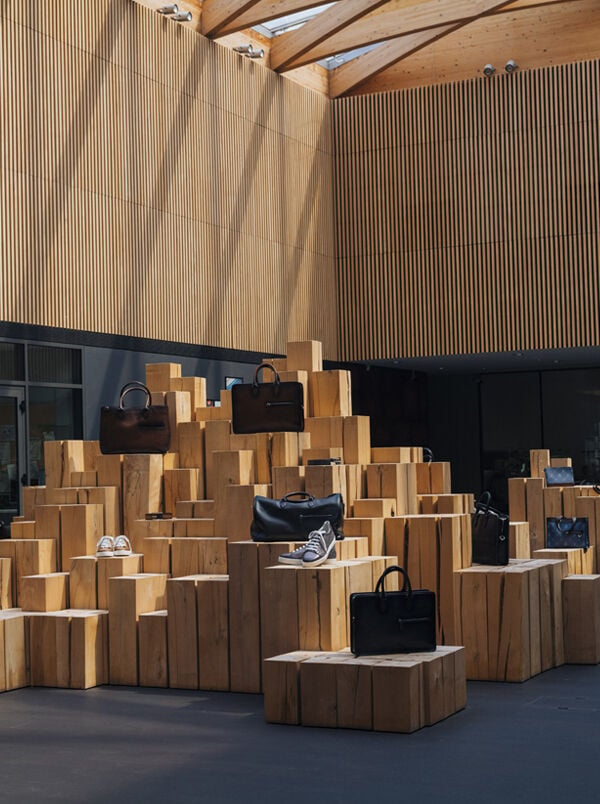
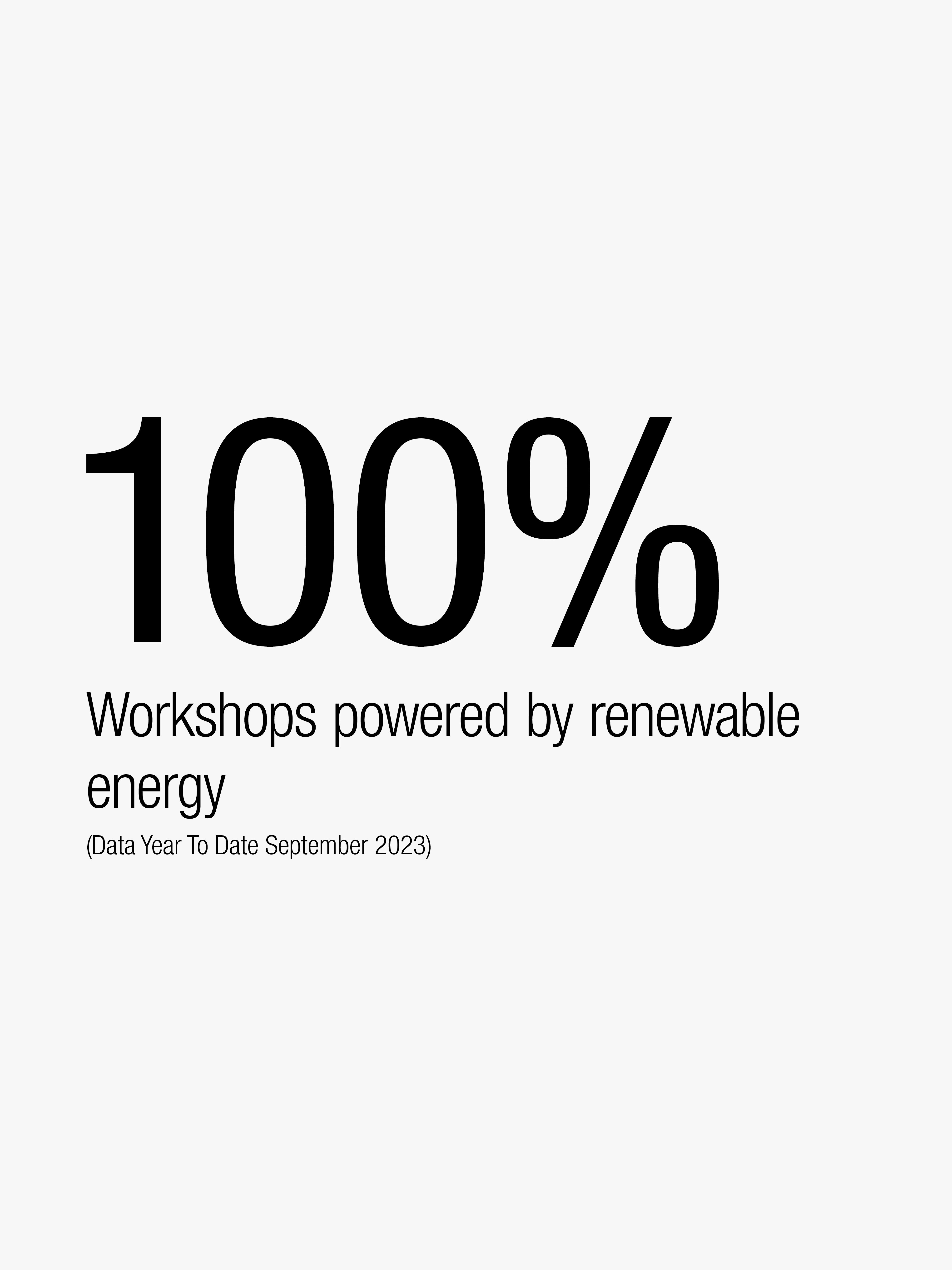
The decision to use renewable energy
The head office, the Bespoke and Services workshops in France, and the Berluti Manifattura have all chosen to use renewable energy sources, based on European Guarantee of Origin certification. A similar approach is gradually being applied to stores. In Ferrara, the roof of the Manifattura is also equipped with solar panels.
Controllable energy consumption
One-third of all Berluti's sites and stores are already equipped with a Smart Impulse box. This smart electricity meter, developed by a French startup, uses advanced algorithms to analyze electricity consumption and better adapt it to actual needs. It can reduce consumption by an average of 15%.
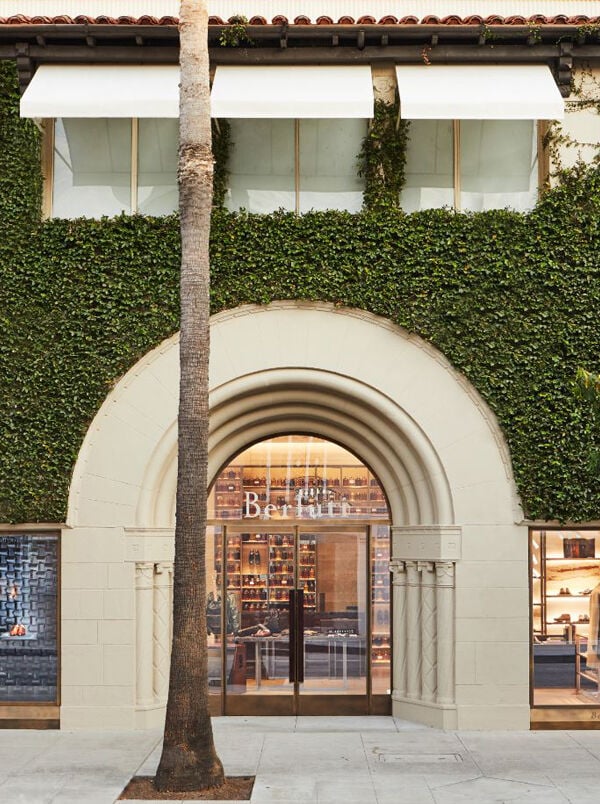
.jpg)
ECO-CONCEPTION AT OUR STORES
To improve the energy performance of the Group’s stores, LVMH created the LIFE in Stores roadmap in 2016. Each year, one of the Maisons is selected for an award in recognition of sustainable innovations in terms of materials, air quality, energy, lighting, and interior decoration. In 2022, the Milan-based Berluti store won the award for Interior Design, which acclaims eco-friendly practices such as the use of certified wood, leather upcycled from scraps, or advanced waste sorting.
In 2023, at the United Nations Climate Change Conference in Dubai, Berluti inaugurated its new store at the Mall of the Emirates, clad and furnished in 100% certified FSC* wood. Berluti is the world’s first luxury store to obtain this certification, which guarantees that the wood used in the store’s cladding and furnishings is taken from sustainably managed forests.
Both awards reflect Berluti’s determination to show more responsible in-store practices.
*Forest Stewardship CouncilLEDs make life more beautiful
A lifespan between 20,000 and 50,000 hours, 60% less power consumption than compact fluorescent bulbs... The decision to use LED lighting is the most logical from an environmental point of view. But because their intensity can be adapted to the circadian cycle, it is also the system that offers the best visual comfort to employees. This is why all sites and stores are gradually being equipped with LEDs, to reach 76% of all coverage by November of 2023.
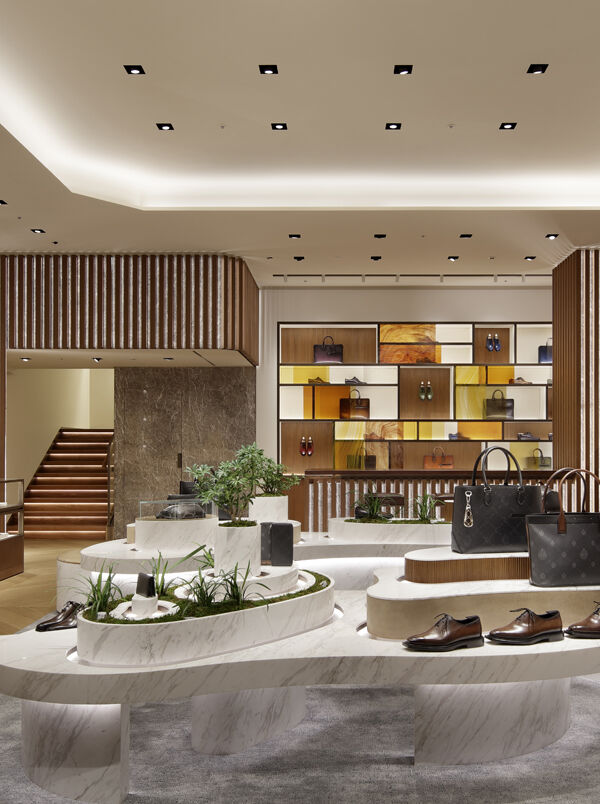
Less waste, better waste
46 tons, that's the amount of CO2 emissions prevented in 2022 by recycling waste at Berluti's French sites.
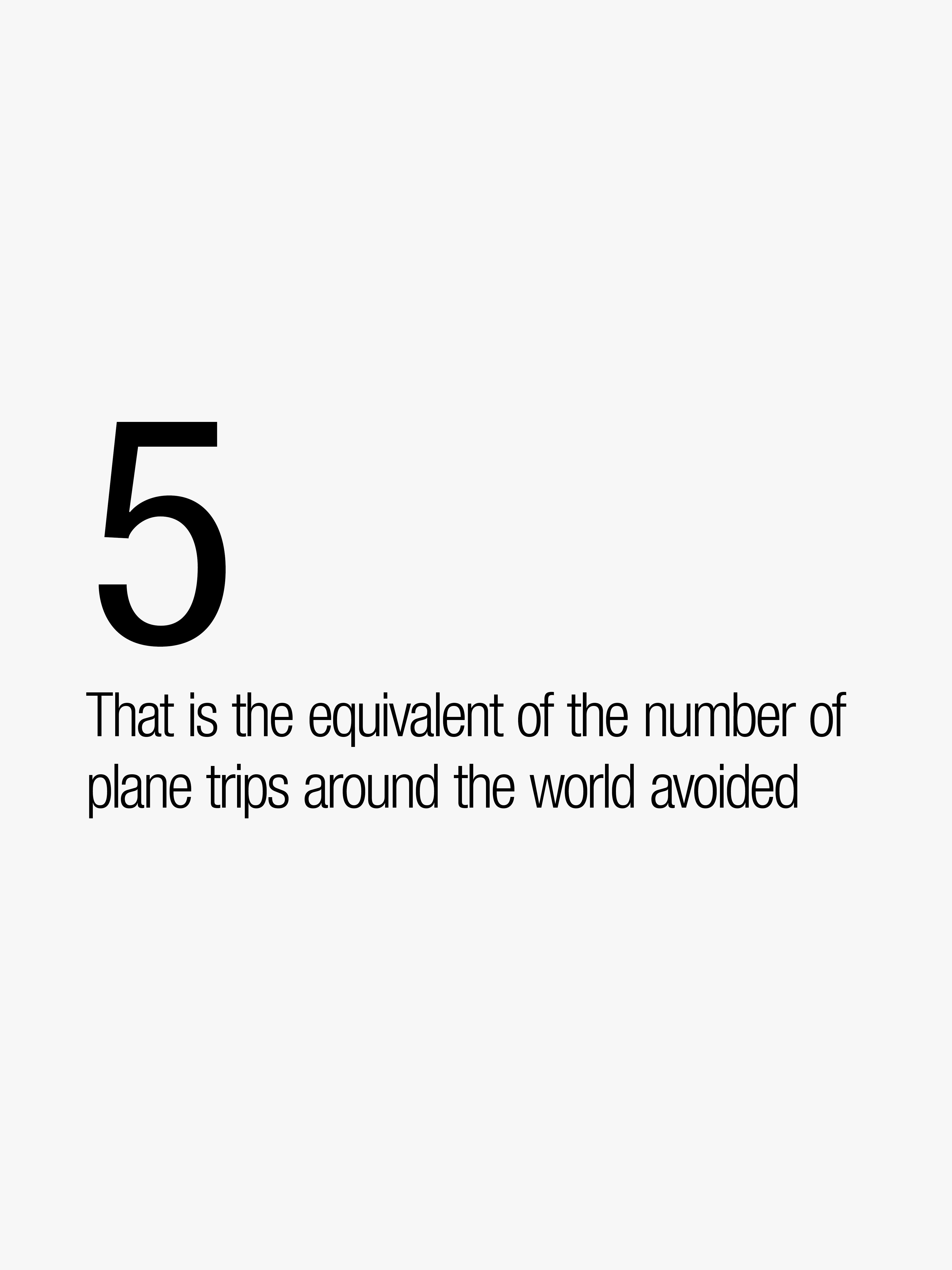
Alternatives to plastic
In today's world, it has become necessary to stop using fossil-origin virgin plastic. The production of this substance, derived from oil, emits a great deal of CO2, which contributes to global warming. Moreover, it also gives rise to various forms of air and land pollution, significantly endangering biodiversity and human health. LVMH has therefore integrated an objective into its LIFE 360 roadmap to completely eliminate all fossil-origin virgin plastic from its packaging by 2030. Berluti is gradually phasing it out.
From recycled plastic to bioplastic to the use of recycled paper, Berluti is progressively adopting substitute materials to replace all use of fossil-origin virgin plastic to reduce its environmental footprint.
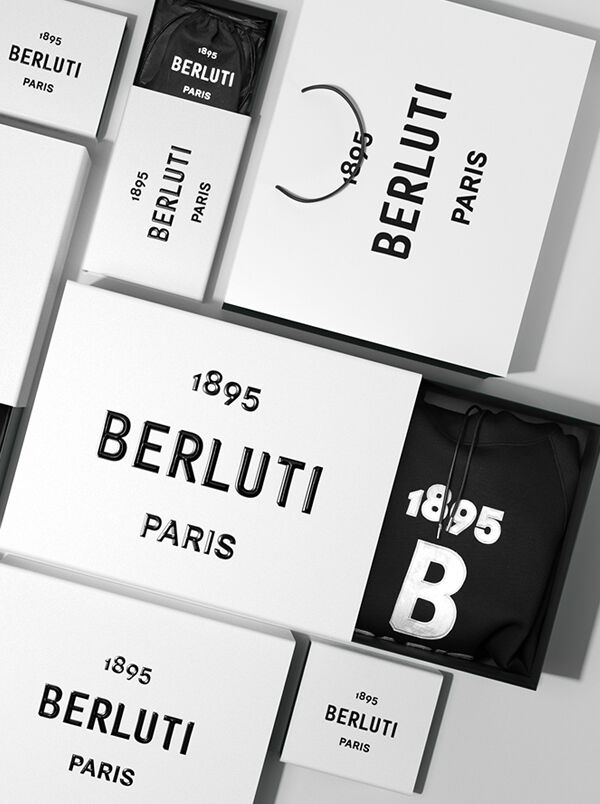
Target of zero virgin plastic by 2030
A virgin plastic is one that is directly derived from the processing of petroleum. Its use is gradually being phased out, in favor of recycled or biosourced plastics and other materials. The boxes and bags provided to clients at Berluti stores contain no plastic. Rather, they are made of cardboard and paper from eco-responsibly managed forests, as well as cotton felt and cords. Little by little, the use of fossil-origin virgin plastic is being relinquished. Half of all logistics packing is already made with recycled cardboard and cotton felt. Since 2022, the bubble wrap used to pack shoes and leather goods, as well as the dust covers used to protect ready-to-wear articles during transport, have been made of plant-based bioplastic.
Eliminating PET (polyethylene terephthalate) water bottles
Since 2022, at more than 95% of our points of sale, the plastic water bottles given out to clients have not been made of fossil-origin virgin plastic. Instead, they have been replaced by tap water ultra-filtered using the Nordaq process, which eliminates impurities and aftertaste while preserving natural minerals. The water is served in washable pitchers and glasses, which are hygienically sealed with a recyclable paper cap. At stores that do not have access to running water, the water bottles are either made of recycled PET or glass.
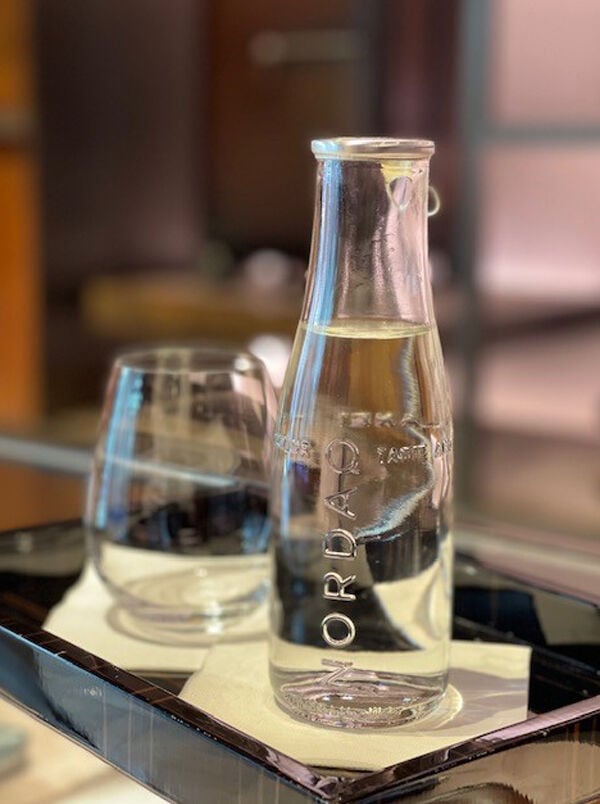